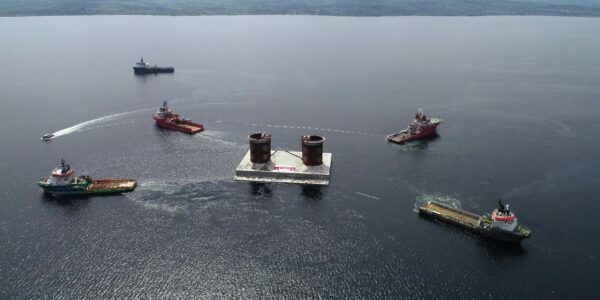
IMMONTEC has more than 25 years of experience in tunnel immersion. Our field of work includes the engineering, preparation, and execution of immersion processes, as well as marine work.
Get in touchIMMONTEC has more than 25 years of experience in tunnel immersion. Our field of work includes the engineering, preparation, and execution of immersion processes, as well as marine work.
Get in touchThe activities of IMMONTEC encompass various phases of the immersion process. While each project has unique dynamics and scope, the work begins with a Design Basis for floatation, transport and immersion, followed by detailed design of temporary facilities, further engineering, and execution preparation.
All engineering and preparation culminate in the final execution by IMMONTEC, involving floating, transporting, and immersing the elements.
The entire immersion operation (OTAO®) is conducted by our experienced staff, emphasizing versatility, innovation, and quality. OTAO®, a registered trademark of IMMONTEC since 1995, stands for Floating, Transporting, Immersion, and Sandflowing. It is the Dutch abbreviation for Floating, Transporting, Immersion and Sandflowing.
During the tunnel element casting process, the necessary temporary provisions are made for the OTAO® process. These provisions include cast-in items such as anchors, ducts, and manholes, as well as recesses, bulkheads, ballast tanks, ballast pipes, temporary supports, the GINA gasket, and pre-stress components. Additionally, part of the pre-calculated amount of ballast concrete or water is added to the tunnel units.
After completing the concrete work, the ballast tanks are filled with water. The tunnel elements are then closed off with temporary bulkheads, and the casting basin dock is inundated. Controlled emptying of the ballast tanks ensures that the tunnel elements begin to float. Once they are floating, the elements can be trimmed and prepared for transport.
Once the tunnel units are floating, tugboats and winches tow the elements to the immersion location. Depending on the towing conditions, additional provisions may be added to the tunnel elements. For example, sea transport requires different measures than river or canal transport due to potentially higher waves. When transporting the Wijkertunnel across the North Sea, the concrete tunnel elements were given extra protection against wave forces.
Once the tunnel element arrives at the immersion location, winches position it horizontally above a dredged trench. The element is attached to immersion pontoons, sheerlegs, cross beams or a combination of these. Simultaneously, a survey system continuously monitors the tunnel element’s position.
The ballast tanks are then filled with water, giving the tunnel negative buoyancy. The element is slowly immersed and connected to the land section or preceding element. It rests on a gravel bed or is temporarily supported with hydraulic jacks for precise positioning. The first watertight seal is achieved using the GINA profile, with a second seal added later using the OMEGA profile.
Read More About Our Innovative SolutionsAn immersed tunnel’s foundation consists either of a pre-laid gravel bed or a temporary support system with space underneath the element. When using temporary support, the space is immediately filled with sand or grout after immersion, creating the final foundation.
Using a sandflow or grout installation, pancake-shaped foundations are formed under the tunnel element. To achieve this, divers attach a pressure pipe to the tunnel’s sandflow system, and the sandflow stops once the supports cover the entire tunnel area. The temporary supports are then released, allowing the tunnel elements to rest on the foundation. Finally, the immersion trench is backfilled, and the top of the tunnel is covered with sand and/or rock protection.
Mission accomplished!