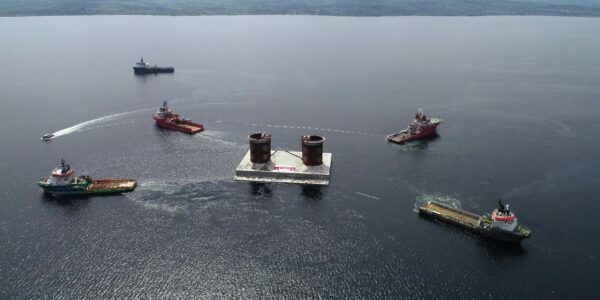
Explore our cutting-edge technologies and methodologies designed to tackle the most demanding engineering and construction projects with precision and efficiency.
Get in touchExplore our cutting-edge technologies and methodologies designed to tackle the most demanding engineering and construction projects with precision and efficiency.
Get in touchFor the Çanakkale Bridge project, the goal was clear: develop a ballast system capable of flawless remote-controlled operations. The challenge was immense—accurately ballasting large floating caissons with high precision and substantial flow capacities, all while maintaining control over the flow, the system, and its distribution.
To meet this challenge, engineers designed two 20-foot ballasting manifolds. These high-tech manifolds featured automated valves and sophisticated pipework, capable of distributing between 1200 and 1300 cubic meters of water per hour. Each manifold could simultaneously manage water distribution to 15 clusters and included a de-ballast pump with a capacity of 1000 cubic meters per hour to efficiently empty the clusters. The system even allowed for the re-distribution of water within the caisson, showcasing its versatility. Over the course of the project, the system successfully pumped a total of 120,000 cubic meters of seawater.
Both the hardware and software were meticulously designed to achieve this high level of performance. The entire ballast system could be controlled remotely through a RAYANT network system. By interconnecting the manifolds—both in terms of pipework and data—a fully redundant system was created, ensuring continuous operation even if one part of the system failed.
Transport and handling of the system were streamlined thanks to its container-sized design. This allowed for easy movement using standard lifting equipment and trucks, facilitating quick and efficient deployment.
This project not only met its goal but also highlighted the power of innovative engineering solutions in overcoming significant operational challenges.
Project 1915 Çanakkale Bridge ProjectWhen the Monaco government tasked NFM and IMMONTEC with the dry maintenance of a crucial 3-meter diameter hinge connecting a floating dike to the mainland, they faced a formidable challenge. The operation required creating a 15-meter deep and 10-meter wide habitat within the confines of a mere 1-meter narrow joint. This task demanded a highly specialized and innovative solution.
The solution came in the form of a U-shaped steel backbone with a box section, inspired by the simple yet effective principle of bicycle tires. This backbone was fitted with four inflatable rubber seals—two at the front and two at the back. In its deflated state, the structure could be maneuvered into the narrow 1-meter joint. Once properly positioned and secured, the seals were partially inflated with water and then topped off with air, reaching a maximum pressure of 3 bars. This created a double watertight seal against both the floating dike and the abutment.
The project presented additional technical hurdles. One key requirement was the casting of an underwater vertical concrete patch with precision deviation of less than 5mm, ensuring a perfectly smooth surface for the seals to adhere to. Moreover, the habitat’s structural design had to withstand the force of 2.8-meter swell waves from the sea. To achieve this, robust locking structures, including cables and cylinders, were implemented to maintain the habitat’s stability.
After meticulous planning and execution, the habitat was operational for three months. During this period, engineers carried out the necessary maintenance on the hinge with precision and efficiency. The successful completion of this project not only addressed the immediate maintenance needs but also demonstrated the capability to perform complex engineering tasks in extremely constrained environments.
This achievement stands as a testament to the innovative spirit and technical expertise of the teams involved, showcasing their ability to overcome significant challenges and deliver effective solutions under pressure.
Project Inflatable Barrier MonacoImmersing tunnels is a complex process that requires highly accurate survey systems and precise control of movements and forces to place tunnel elements within tight tolerances. To enhance safety and efficiency by limiting manual operations within the tunnel during immersion, a remote-controlled immersion system was developed for the Busan Geoje project in South Korea.
The core of this system was to centralize critical operations on a single command vessel, the main immersion pontoon, from which all essential systems could be operated remotely. This innovative approach allowed for seamless control over several key aspects:
This remote-controlled system significantly reduced the need for manual intervention within the tunnel, enhancing safety and efficiency during the immersion process.
The successful implementation of this system in the Busan Geoje Fixed Link project demonstrated the effectiveness of remote-controlled operations in complex engineering tasks, setting a new standard for tunnel immersion techniques.
Project Busan Geoje Fixed LinkWith the growing demand for offshore wind energy, especially in depths of 40-80 meters, new technologies are being developed to support this expansion. One such innovation by IMMONTEC is a method for installing Gravity Based Foundations (GBFs) without the need for floating cranes or lifting equipment.
This groundbreaking method relies on a remote-controlled ballasting system. The system fills the chambers inside the GBF in a controlled manner, allowing for installation with vertical accuracy within 5-10 centimeters, even in challenging conditions with winds up to 7 Beaufort and waves of Hs 1.5 meters.
A key aspect of this method is the use of a 3 or 4-point line and anchor system. Standard anchor handling tugs are positioned in line between the anchor and the GBF, ensuring the horizontal plane position is controlled within 5-10 centimeters of the target location, depending on environmental conditions.
This innovative system has been successfully deployed in several high-profile projects, including the installation of five 6500-ton GBF structures off the coast of Blyth, UK, and the installation of two 60,000-ton caissons in the Dardanelles Strait near Çanakkale, Turkey.
These achievements highlight the effectiveness and precision of IMMONTEC’s method, offering a reliable solution for the installation of large offshore structures without the need for traditional lifting equipment.
Project Blyth Offshore Wind DemonstratorThe successful immersion of tunnel elements depends on the precise positioning of these elements in relation to their theoretical alignment. This task becomes particularly challenging in extreme conditions, such as large depths, high winds, and strong currents, often leading to significant operational cancellations and downtime.
To address these challenges, an External Positioning System (EPS) was developed. This innovative system consists of two portal-shaped “legs” that are attached to the roof of the tunnel element. Once the element is roughly placed on the seabed (gravel), the hydraulically operated legs are activated, allowing for autonomous fine-positioning.
This system ensures that tunnel elements are positioned securely and with high accuracy within the set tolerances, even under design wind and current conditions. The EPS significantly reduces downtime and operational cancellations, ensuring the successful and efficient immersion of tunnel elements in challenging environments.
Project Busan Geoje Fixed LinkDo you have a challenging project and need a reliable ally? With over 25 years of experience, we guarantee our clients and partners top quality and maximum risk management in the construction and maintenance of civil infrastructure.